In this post, let’s delve into some commonly asked questions:
- What does ‘linearity’ mean?
- How does it differ from nonlinear simulation?
- When is nonlinear simulation necessary?”
First, let’s explore the concept of linearity:
Linear static simulation is a fundamental type regularly conducted by engineers and designers.
The concept of linearity closely relates to proportionality. In linear simulation, when applying a force to a model and calculating outcomes like displacements, stresses, and strains, you’re analyzing results for that specific force value. However, linear simulation enables extrapolation to an infinite range of force values.
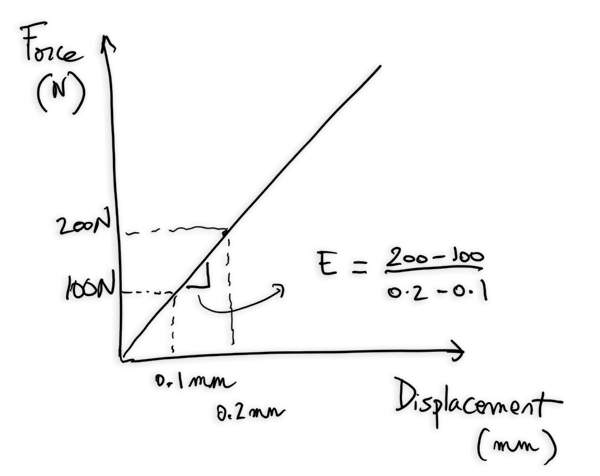
What I’m getting at is that in linearity, if you scale the input force by a certain factor, the resulting outcomes are also scaled by the same factor. This relationship illustrates the essence of linearity.
Essentially, there’s a proportional connection between the applied force and the observed results.
Why does this occur?
In linear simulation, several crucial assumptions are made, particularly regarding the material model employed to simulate real-world materials.
What exactly is a material model?
In reality, materials are never just homogenous blocks of matter; they possess intricate microscopic structures filled with numerous imperfections.
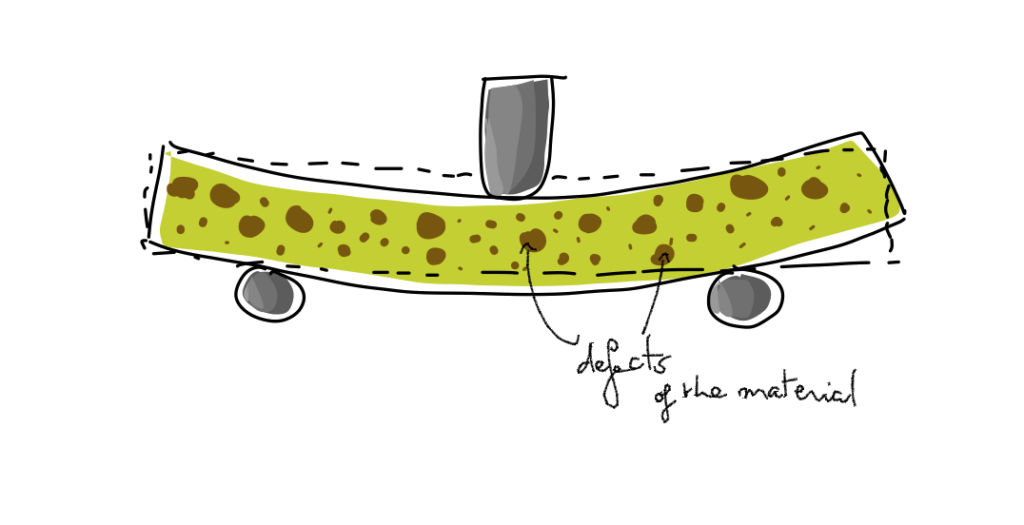
However, certain materials, such as steels, can be reasonably approximated as isotropic blocks of matter. When we confine our analysis to small deformations, we can define these materials by establishing a relationship between stress and strain.
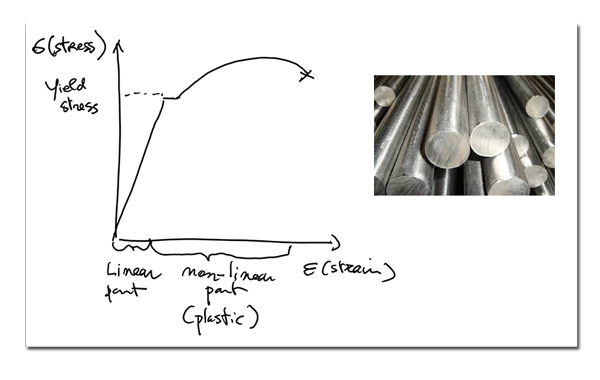
This is termed as an elastic material model, enabling us to establish a linear correlation between stresses and strains.
Hooke’s law encapsulates this relationship between stress and strain, relying solely on two coefficients: the Young’s modulus and the Poisson’s ratio.
When can I use linear simulation? If your simulation purpose is to analyse several design variations to compare the difference between the designs and you stay within small deformations at all times, then you can use safely linear simulation.
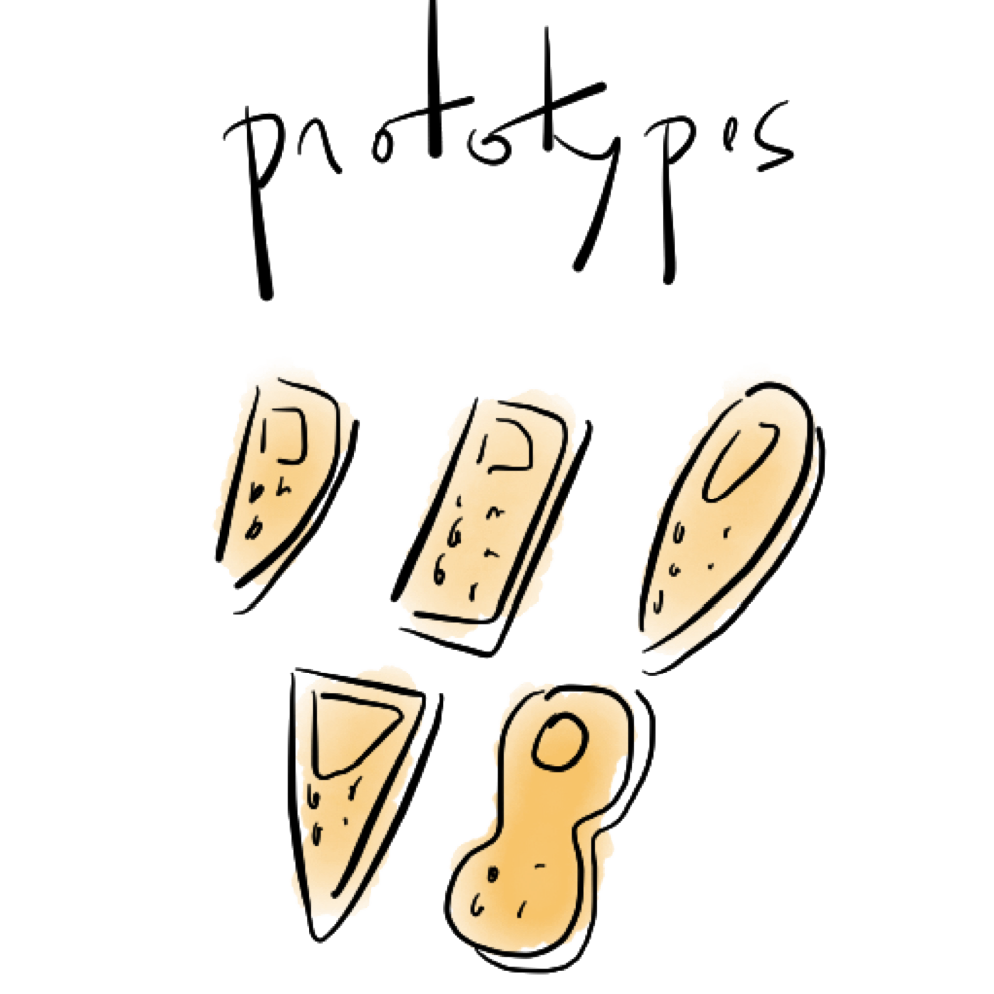
Linear simulation provides a safety factor, offering insight into the relative safety of your design compared to others.
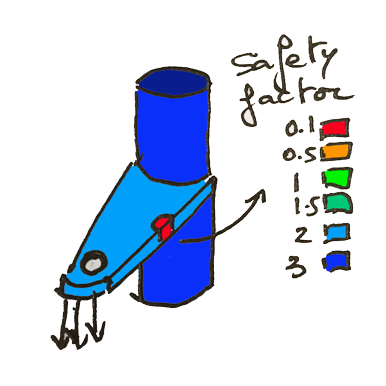
However, if you observe that stresses and displacements exceed expected values, it could signal issues with your simulation settings or indicate the necessity to transition to a nonlinear simulation approach.
When do I need to use nonlinear simulation?
The primary reason for transitioning to nonlinear simulation arises when small deformations can no longer be maintained. When intending to apply significant loads and accurately simulate failure behavior, the assumptions inherent in linear simulation become invalid. Thus, nonlinear simulation, incorporating nonlinear material models, becomes imperative.

At this stage, complexities arise as nonlinear simulation necessitates considerations beyond those required in linear simulation. These include:
- Nonlinear Material Models
- Nonlinear Contacts
- Large Deformations
Moreover, nonlinear simulation isn’t as straightforward as linear simulation, requiring more time and effort to execute.
Put simply, a linear simulation boils down to solving a large matrix inversion problem, often with millions of degrees of freedom. While computationally intensive, modern computers can typically handle this in a single iteration using methods like LU decomposition.
In contrast, nonlinear simulation introduces the concept of iterations and convergence. Achieving a solution involves computing a series of matrix inversions, each with its own level of error, which can either converge or diverge depending on your simulation model setup.
This process demands more time and expertise to:
- Construct a model that ensures convergence.
- Obtain results that closely resemble reality by employing appropriate nonlinear material or contact models